About Alcast Company
Table of ContentsAll About Alcast CompanyThe Best Strategy To Use For Alcast CompanySome Of Alcast CompanyIndicators on Alcast Company You Need To KnowWhat Does Alcast Company Do?Not known Facts About Alcast CompanyAlcast Company - Questions

If you assume that a wrought alloy might be the very best for your job, have a look at some of our write-ups that discuss more concerning specific functioned alloys, such as Alloy 6061 and Alloy 6063. On the other hand, if you believe an actors alloy would certainly be better for you, you can find out more regarding some cast alloys in our Alloy 380 and Alloy 383 posts (coming quickly).
Unknown Facts About Alcast Company

Having the experience and market expertise to craft your spreadings for optimal production and high quality results will certainly improve the project. Producing light weight aluminum spreading needs a facility collection of processes to attain the best results. When picking a brand-new aluminum foundry to partner with, guarantee they have substantial sector experience and are well-informed regarding all facets of the aluminum casting procedure: layout, production, material evaluation, and item testing.
(https://disqus.com/by/disqus_S18EMely1h/about/)The foundry ought to also have a tested record of providing extraordinary products that meet or exceed consumer assumptions. Quality control must additionally be at the top of your list when selecting a light weight aluminum foundry. By dealing with a certified foundry who follows the requirements for high quality control, you can secure the integrity of your product and guarantee it satisfies your requirements.
The smart Trick of Alcast Company That Nobody is Discussing
By choosing a firm who provides solutions that satisfy or exceed your product demands, you can be sure that your job will certainly be finished with miraculous accuracy and efficiency. Certain aluminum shops focus on particular sorts of producing procedures or casting techniques. Different parts need different production strategies to cast aluminum, such as sand spreading or pass away casting.
Pass away casting is the name offered to the procedure of producing complicated metal parts with use molds of the part, likewise referred to as dies. The procedure uses non-ferrous steels which do not have iron, such as light weight aluminum, zinc and magnesium, due to the preferable properties of the steels such as low weight, greater conductivity, non-magnetic conductivity and resistance to corrosion.
Excitement About Alcast Company
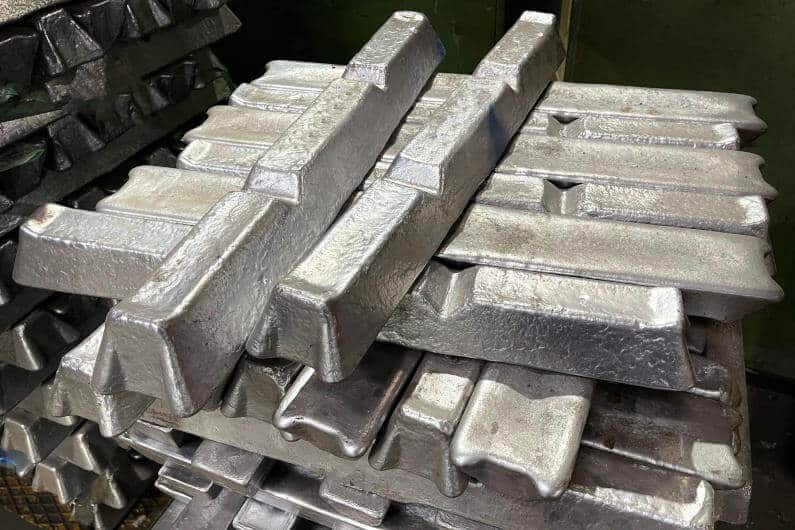
No matter redirected here the sub-process, the die casting process can be broken down right into 6 steps. After the pureness of the alloy is checked, passes away are created. To prepare the needs spreading, it is very important that the dies are tidy, so that no deposit from previous productions stay. After cleaning, the ejection lubrication is applied to the die to make sure a smooth launch.
The pure metal, additionally referred to as ingot, is added to the heating system and maintained the molten temperature level of the steel, which is after that moved to the injection chamber and infused right into the die (aluminum metal casting). The stress is then preserved as the metal solidifies. When the steel strengthens, the cooling procedure starts
The 5-Minute Rule for Alcast Company
The thicker the wall of the component, the longer the cooling time as a result of the amount of interior metal that also requires to cool. After the part is completely cooled, the die halves open and an ejection device presses the element out. Following the ejection, the die is closed for the next injection cycle.
The flash is the extra product that is cast during the process. This should be trimmed off using a trim device to leave just the major component. Deburring eliminates the smaller items, called burrs, after the trimming process. The element is brightened, or burnished, to provide it a smooth coating.
Our Alcast Company Ideas
Today, top makers make use of x-ray testing to see the whole interior of elements without reducing into them. To get to the completed item, there are three primary alloys used as die spreading material to choose from: zinc, light weight aluminum and magnesium.
Zinc is one of the most pre-owned alloys for die casting due to its reduced cost of raw products (Casting Foundry). Its deterioration resistance likewise permits the elements to be long lasting, and it is one of the extra castable alloys due to its lower melting factor.
Indicators on Alcast Company You Need To Know
As pointed out, this alloy is one of one of the most typically utilized, yet makes will, at times, pick light weight aluminum over zinc because of light weight aluminum's manufacturing benefits. Light weight aluminum is extremely economical and among the more versatile alloys. Light weight aluminum is used for a variety of various items and industries anything from home window frames to aerospace materials.